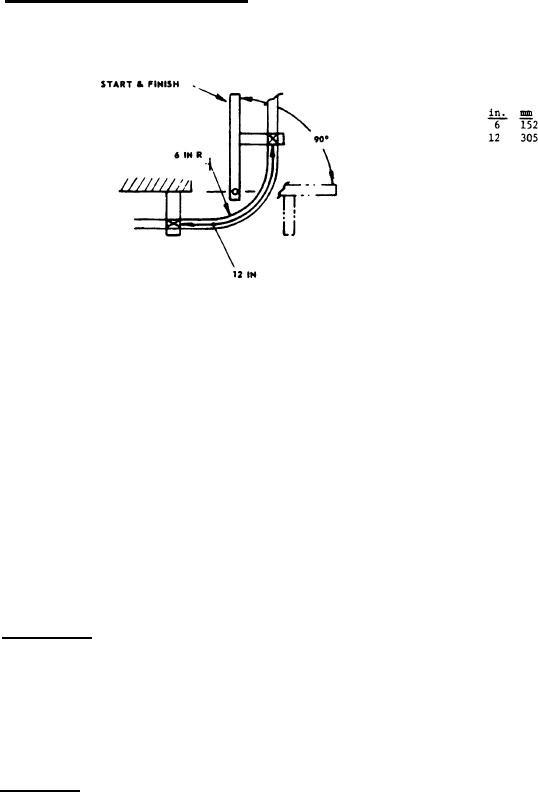
MIL-C-82630(OS)
4.5.7 Cold temperature (90-degree bend test). While the cable is mounted in a suitable
fixture, a 90-degree bend test shall be performed at -40 ±3 degrees (-40°±2°C), The cable
assembly and test fixture shall be conditioned at the test temperature for at least 12 hours
prior to initiation of the test.
Figure 4.
Test Setup - 90-Degree Bend, Low Temperature.
The cable shall be mounted and clamped at two points on the test fixture such that a 90-degree
bend with a radius not to exceed 6 inches (152mm) shall be formed within a 12-inch (305-mm)
length of cable (see Figure 4). The cable shall be rididly secured to the underside of a
fixed support lying in a horizontal plane at one clamp position, and rigidly secured to a pi-
voting arm which shall be so mounted as to oscillate from a vertical position to a horizontal
position. When in its horizontal position, its axis shall form an extension of the plane
of the fixed support, and the cable shall be attached to the underside of the arm. The at-
tachment of the cable to the oscillating arm shall be made when the arm is in the vertical
position. The pivot axis of the oscillating arm shall intersect the longitudinal axis of the
fixed support and shall be equidistant from the two clamping points. The fixture shall be so
designed that the section of cable between the clamp positions shall not touch any portion of
the mechanism or cold box during the test.
One cycle of test shall consist of an oscillation of the pivot arm from the vertical position
to the horizontal and back to the vertical. The test shall be conducted at a rate of one
cycle per minute with each half cycle to be accomplished within 6 seconds. The delay between
cycles may occur at the end of either half cycle or may be divided to occur at the end of each
half cycle.
Continuity of all conductors shall be monitored continuously. The test shall be stopped and
the number of cycles recorded in the event of failure of any conductor. The test shall con-
sist of 500 cycles of bending. At the conclusion of this test, the cable shall be subjected
to the test of 4.5.4.
4.5.8 Cable strength. The cable shall be securely clamped at two points along its length
15 inches apart. The equipment shall be oriented such that the axis of the 15-inch (380-mm)
length of cable is in a horizontal plane. At a point midway between the clamps, a weight of
300 pounds (1335 N) shall be suspended from the cable for a period of at least 60 seconds,
not including the application and removal periods. The shoe or weight support shall be no
more than 1-1/2 inches (38mm) wide and of such design as to spread the load over the 1-1/2-
inch (38mm) length of cable. The cable sheath may be protected or padded to spread the
load and prevent damage to the cable sheath. The load shall be applied and released a total
of 20 times over a period not to exceed 2 hours. At the conclusion of the test, all con-
ductors in the cable shall be tested for continuity and the cable shall be subjected to the
test of 4.5.4.
4.5.9 Torsion test. While it is mounted in a suitable test fixture, a torsion test shall
be performed on the cable assembly. The cable shall be mounted and clamped at two points on
the test fixture such that a 90-degree bend with a radius not to exceed 4 inches (102mm) shall
be formed within a 10-inch (254-mm) length of cable (see Figure 5). The cable shall be
rigidly secured to a fixed support at one clamp position, and rigidly secured to a pivot arm
at the second clamp position. The pivot axis of the arm shall be an extension of the center-
line of the cable shich is clamped to the fixed support.
9
For Parts Inquires call Parts Hangar, Inc (727) 493-0744
© Copyright 2015 Integrated Publishing, Inc.
A Service Disabled Veteran Owned Small Business